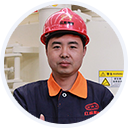
您好,新型干法水泥生产线是以生料预均化技术和回转窑煅烧技术为基础,以悬浮预热和窑外分解技术为核心的现代化水泥生产方法,其工艺的特点是生产能力大、自动化程度高、产品质量高、能耗低、有害物排放量低、工业废弃物利用量大。
“两磨一烧”——即是生料制备、熟料煅烧、水泥粉磨,生产优质水泥,需严格按照规定程序进行操作,经过一系列程序的加工,方可达到优质水泥成品,新型干法水泥生产工艺是目前常用的水泥生产工艺,具体生产设备及工艺流程如下:
一、生料制备
1、原料破碎、预均化(石灰石、黏土、铁粉、萤石、石膏)制造水泥的主要原料是石灰石、黏土、铁粉、萤石、石膏,通过爆破或者截装机将原料提取,使用破碎机将这些原料进行破碎,根据原料的硬度选择合适的破碎机,较硬矿料选择颚式破碎机,较软矿料选择反击破,几种原料经过破碎之后送入原料堆场进行预均化,原料必须经过调配和混合,使其成分符合生料需求,原料均匀化堆场需覆盖,以免受外界环境影响。
2、湿料烘干
对于生料中湿度较大的原料,需在破碎处理之后采用烘干机进行烘干处理,烘干之后才能进入磨机内进行细磨,烘干机一般选用转筒烘干机或者热风烘干机。
3、球磨磨碎
采用配料计量称对原料进行计量,使用球磨机或者立式磨机对生料进行磨碎处理,球磨机利用钢球的冲击作用将原料磨碎,由于生料磨耗电大,目前使用量少,球磨机磨矿能力强,环保节能,常用于磨矿阶段,此时使用煤磨机将原煤进行磨碎处理,对煤粉进行集尘处理,石膏经过破碎加工之后也需进行磨矿处理,并对原料进行集尘处理。
二、熟料煅烧
1、生料预热、增湿
生料经过磨矿处理之后,进行预均化,喂料计量确定合适的调配比例,之后进入预热器进行预热处理,同时进入增湿塔进行增湿处理,以立式预热器和旋风预热器为主,原料通过预热分解,达到分散、气固分离、预分解的目的,窑尾预热器出来的烟气一路进入增湿塔进行降温增湿,一路进入磨机中作为烘干热源,出磨烟气与出增湿塔烟气混合进入集尘器中。
2、熟料煅烧、冷却,进入熟料库
经过预热后,生料浆进入回转窑窑体内进行煅烧,在窑内与气体发生热交换,依次发生干燥,脱水、盐分分解、固相反应、熟料烧成、冷却、制成熟料等环节,回转窑内依次形成干燥带、预热带、硅酸盐分接待、放热反应带和烧成带,煤块经过回转窑煅烧之后,进入分解炉分解。干法煅烧生料的优点是节能、产量高、质量稳定、环保、生产率高,熟料烧成后进入冷却机进行冷却处理,之后进入熟料库储存。
三、水泥粉磨
1、配料计量,水泥粉磨
经过煅烧、冷却之后的水泥熟料进行配料计量,调配合适比例之后进入水泥磨中进行粉磨加工,同时加入石膏,水泥磨为卧式旋转结构,采用耐磨钢球作为磨矿介质,钢球分为多种规格,分别进行粗碎和细磨,对水泥原料进行精细化的粉磨加工,水泥磨对于物料的适应能力强,可连续生产,磨碎比大,粉磨细度易于调节,可实现粉磨与烘干同时进行,经过粉磨加工之后,可得到成品水泥。
2、水泥包装
水泥制成之后进入水泥库中进行储存,可采用汽车散装或者火车散装,也可采用包装机进行包装形成袋装水泥,使用汽车运输。
水泥生产过程中,涉及到原料集尘、煤粉集尘、电收尘、水泥集尘等程序,每个阶段都配置收尘装置,处理后粉尘排放浓度可降低至50毫克每立方米以下,以现今的环保、热工、粉磨、均化、储运、在线检测、信息化为技术装备基础,实现废料、废渣循环利用,促进循环经济和可持续发展。
感谢您对红星机器的支持和信任!